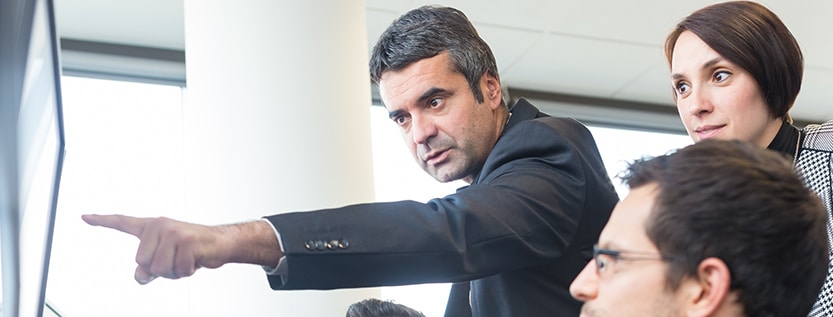
System Simulation
Software-supported simulation of TGA systems
The costs for the construction and operation of buildings are constantly growing, not only because of the general price development (keyword heating and electricity costs), but also because modern technical systems have many advantages, but are also expensive. A system simulation helps to save costs.
What is a system simulation?
System simulation is a sub-area of building simulation. While the building simulation creates a virtual model of the entire building in the computer, a plant simulation deals with a technical system and the interaction of its components. In a plant simulation, the system is put into operation as a computer model and different scenarios are tested.
With a system simulation, for example, heating systems, ventilation systems, air conditioning or fire alarm systems are tested. System simulation can be applied in office buildings as well as production facilities and single-family homes.
How does the system simulation work?
A virtual model of the system is created on the computer using special software. The program is based on modules and can therefore be extended almost indefinitely and adapted exactly to the conditions on site. The system simulated in the computer is put into virtual operation and tested for efficiency and weak points.
This is possible because all technical parameters of the components are incorporated into the system and their interaction with each other is also taken into account. These include, for example, the maximum speed of electric motors or the maximum pressure load of pipelines or the service life of ball bearings and many other factors.
How are system simulations applied?
The range of applications is very broad. With the help of system simulation, for example, simple calculations of load or capacity can be made. This refers to how heating or ventilation must be dimensioned in order to achieve a pleasant indoor climate. But this is only the starting point. System simulation allows much more complex issues to be examined.
For example, it can determine which weak points the technical system has by simulating continuous operation that does not occur in practice or only very rarely. In reality, such a test would probably not be possible because it would be too expensive and could cause the system to fail. In the plant simulation it becomes clear how powerful the system is in continuous operation and which components fail first.
Other tests can only be carried out in the system simulation. These include the behaviour of the system under extreme conditions such as very high or low temperatures or in the event of prolonged rain and similar conditions. The effects of aging and material fatigue can also be simulated very well in a system simulation.
System simulation is particularly important for safety engineering plants, as a real test under real conditions is hardly possible in practice.
What are the benefits of system simulation?
It supports to save costs, because with its help the system can be adequately dimensioned. Without system simulation, capacity reserves must always be planned for special cases, but those are almost never needed in practice. They cost money, which can be saved if the optimum capacity is selected with a system simulation. In addition, system simulation can reveal the weak points of the system and thus reduce the costs for maintenance and servicing. For example, minor changes can reduce the susceptibility to failures and improve the service life of the technical system. Simulated operation under extreme conditions increases safety because the TGA engineer knows how the system will behave under such conditions.
Summary
The system simulation is a virtual operation of a technical system, which is simulated as a computer model. It offers many advantages and helps to reduce disturbances and increase efficiency. Unfortunately, system simulation is still applied far too rarely because many people responsible in the construction industry have not recognised its potential yet.